PRESSING
CNC HYDROULIC PRESS – 3KW
Specification
250 Ton
3500 mm width – Hydroulic Press
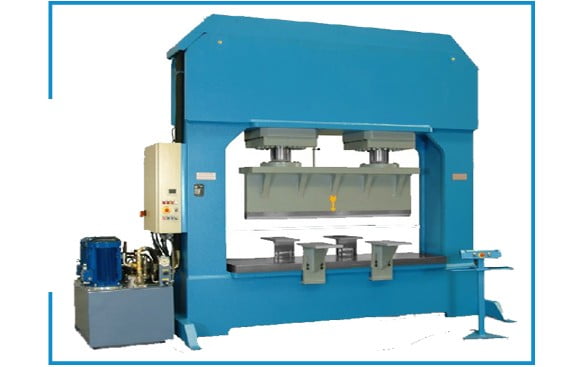
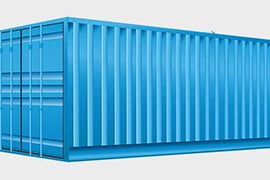
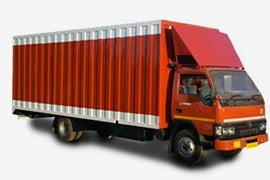
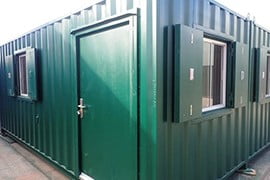
Pressing
Most contemporary machine presses normally use a mix of electrical motors and hydraulics to attain the essential pressure. Arrived the growth of the dies. Historically, metal has been formed by hand using a hammer. Afterwards, bigger hammers were built to press more metal simultaneously, or even to press thicker stuff.At our Press Shop, we manufacture various press shop parts like tanks ranging from 5 litres to 1200 litres in capacity, air / water / oil filters, cooling fans for engines, off-road engines, and more for OEMs. We specialise in manufacturing all types of sheet metal components for OEMs.
Reduce hammers and excursion hammers use a mechanism to raise the hammer, and subsequently drops by gravity on the job. From the mid 19th century, both guide and rotary-cam hammers started to be substituted in business by the steam hammer, which had been first described in 1784 by James Watt, a Scottish inventor and Mechanical Engineer who contributed to the oldest steam engines and condensers, but not assembled till 1840 by British Inventor James Nasmyth. From the late 19th century, steam hammers had improved considerably in size; in 1891 that the Bethlehem Iron Company created an improvement letting a steam hammer to provide a 125-ton blowoff.
Pressing Machine in Coimbatore utilize strain to generate or modify the design of alloys utilised in Fabricating. Pressing Machine utilize about three distinct procedures of communicating alloy mechanical, acoustic and hammering. Utilized strain is utilised to lower or form sheet metals. Additionally, a few media equipment may punch holes materials. Pressing Machines use three different methods of processing metal: mechanical, hydraulic and forging in GKindus.
We produce DG set canopies, tanks for DG sets, specialised components for sheet metal assemblies and more for OEMS. Our production process can be customised to your needs.
With our latest CNC technology, we are able to work with a wide range of materials like sheet metal, bulletproof material, metal, plastic, brass, rubber, marble, titanium, aluminium, composite materials, and more.
We produce DG set canopies, tanks for DG sets, specialised components for sheet metal assemblies and more for OEMS. Our production process can be customised to your needs.
A press brake is a machine pressing tool for bending sheet and plate material, most commonly sheet metal.It forms predetermined bends by clamping the workpiece between a matching punch and die.Typically, two C-frames form the sides of the press brake, connected to a table at the bottom and on a movable beam at the top. The bottom tool is mounted on the table, with the top tool mounted on the upper beam.
There are several types of brakes as described by the means of applying force: mechanical, pneumatic, hydraulic, and servo-electric.
In a mechanical press, energy is added to a flywheel with an electric motor. A clutch engages the flywheel to power a crank mechanism that moves the ram vertically. Accuracy and speed are two advantages of the mechanical press